The Project
Impressions from the project process
Project Information
Requirements
Working scaffold for unrestricted access to the pieces being tested Realization of different platform levels at heights between 7.00 m and 10.50 m Modifications could be carried out to the load-bearing steel construction as well as the 88 inclined-arranged hydraulic cylinders 2.5 kN/m² live load
Solutions
3D scaffold planning with the help of PERI CAD identified all obstructions and minimized these well in advance Scaffold basic grid: 2.00 m x 1.50 m Detailed and early coordination of the scaffolding concept with the users and scaffold erection team VARIOKIT bridging construction above the wings Integrated stair access with 1 m wide flights of stairs
Customer benefits
Optimal adjustment of the working levels required for the fuselage and wings – whilst taking into account the steel and hydraulic constructions as well as ensuring that all access points were kept clear
Modifications with system components in 25-cm increments – without any time-consuming tube-and-coupler assembly
Reduced surface weight
System combination of PERI UP with VARIOKIT
show more
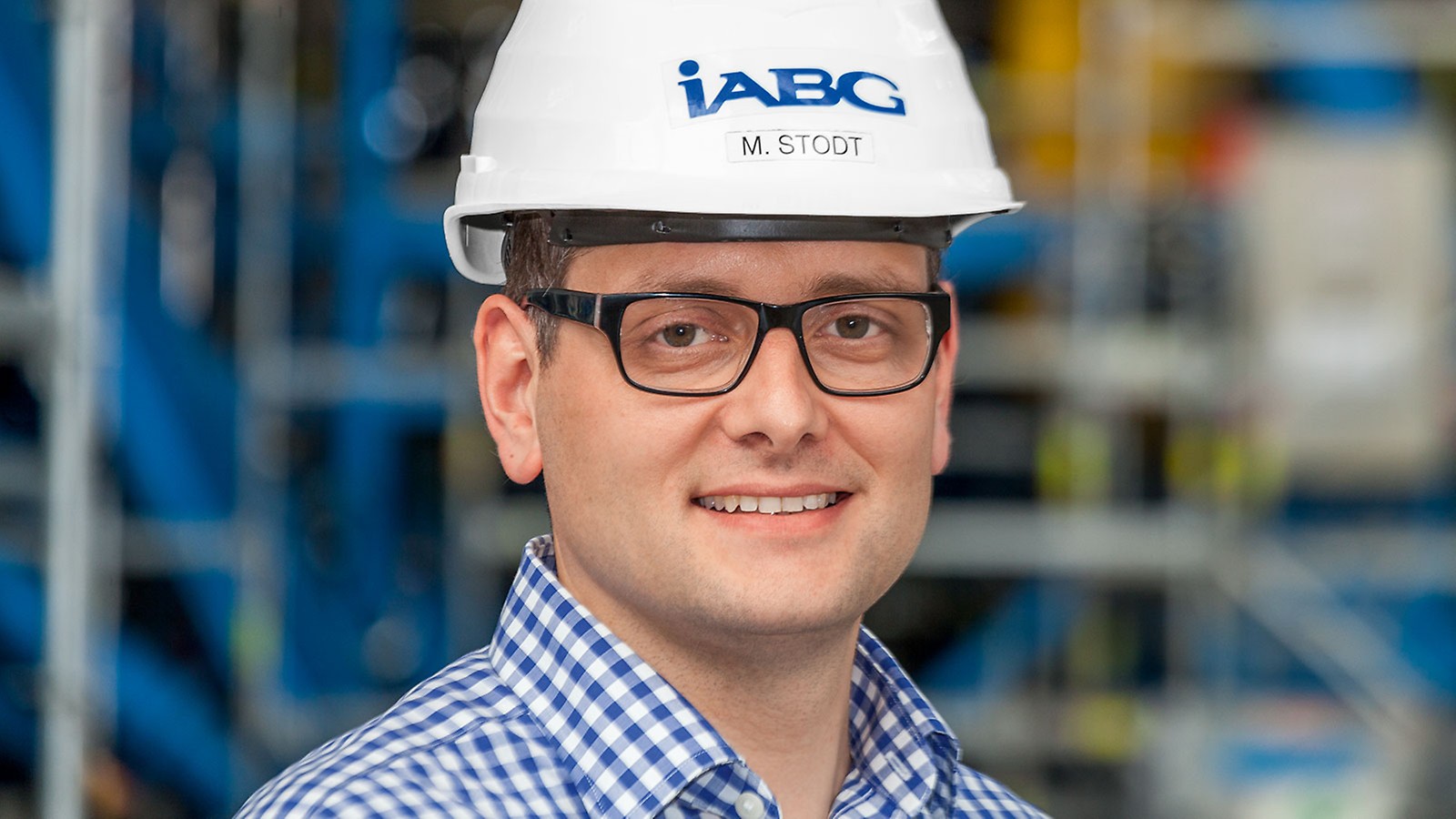
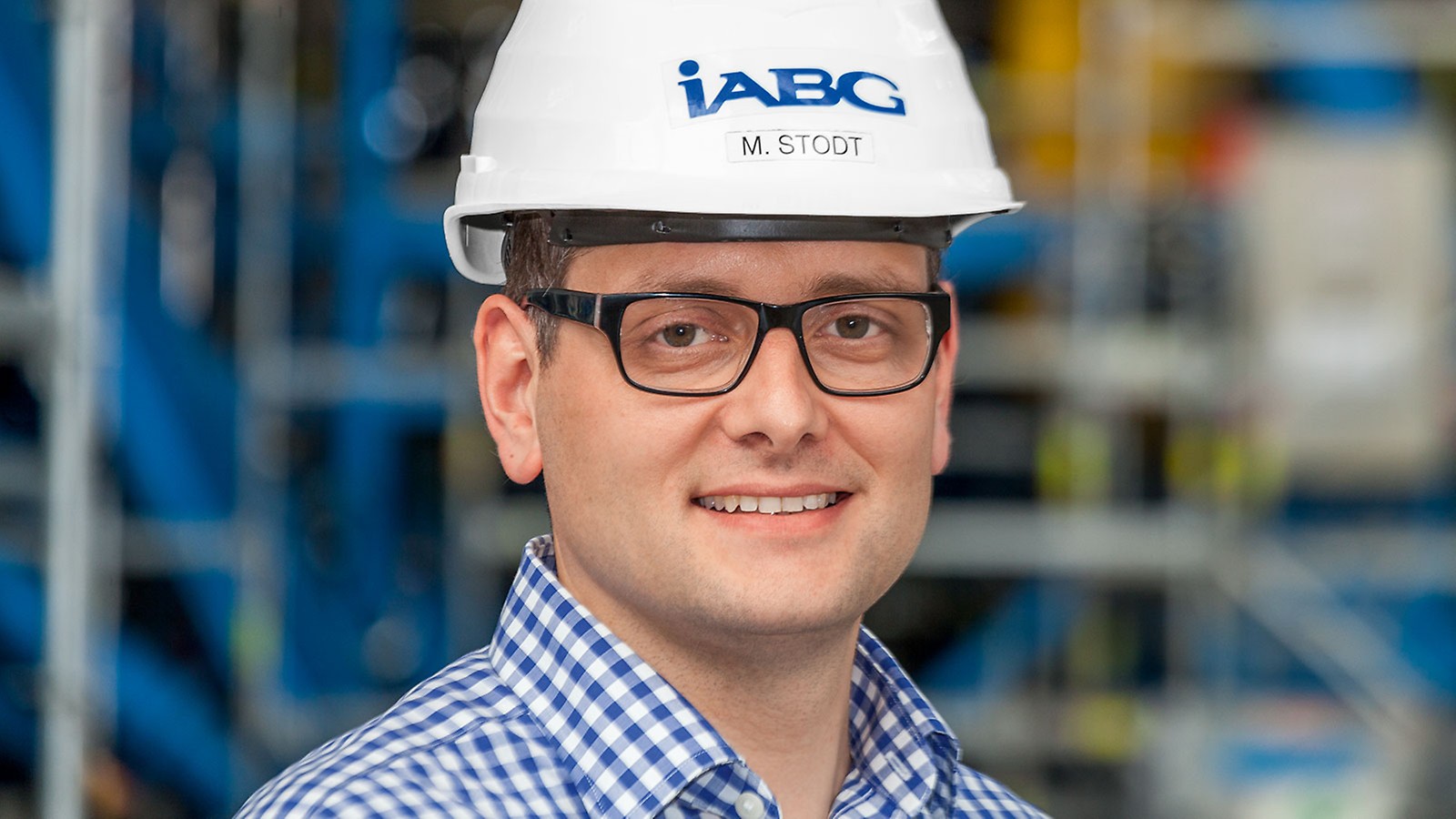
Michael Stodt
Head of Aircraft Structural Testing at IBAG
The recipe for success is the modularity and adaptability of the PERI UP scaffolding system – as well as the combinability with other products in the PERI portfolio. Furthermore, the project support provided by the PERI engineers was very professional and extremely positive.
Are you working on a project like this?
Call us on +966 (0) 11 230 0655 to discuss your requirements further.
Location